The demand for automotive spare parts has increased immensely due…
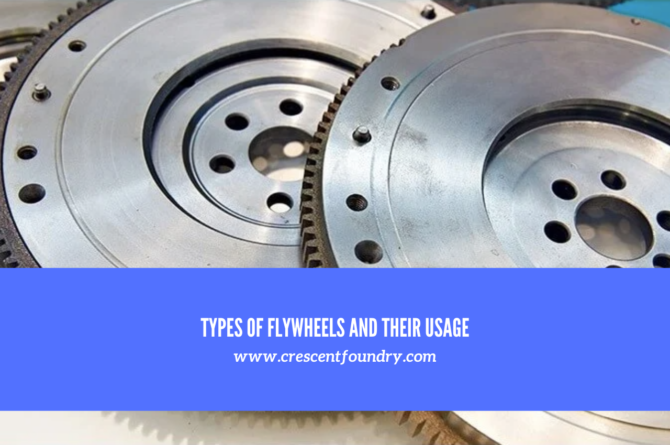
Types of Flywheels and Their Usage
While not often talked about, flywheels are extremely important components of automobiles. There are various applications of the flywheel in the automotive industry, as well as in many other industries. In essence, flywheels are relatively heavy disks of metal that are fitted to the crankshaft rear-end (ideally, between the transmission and the vehicle engine). These disks typically have high levels of rotational inertia, which helps in counteracting sudden speed changes/fluctuations. The additional rotational energy is stored for usage later, energy pulses are smoothened, and the pistons receive the requisite energy. In order to ensure that vehicular engines operate smoothly and at constant speeds, the top flywheel manufacturers in India and abroad offer different types of flywheels – each with its specific features and advantages.
Here’s a roundup of the different types of flywheels and their usage:
Solid Disk Flywheels
A solid disk flywheel is, broadly speaking, a circular solid disk that is generally used in cast iron single flywheel thresher systems. Leading flywheel manufacturers in India implement precision technologies to finalize the size and dimensions of solid disk flywheels – so that they perform as required. Several key parameters are taken into account while designing these flywheels.
Two different types of stresses are used in solid disk flywheels – radial stress and tangential stress. These high-utility tools typically have a disk and a hub section. In order to get a proper idea about the usability of a solid disk flywheel, its ‘mass amount of inertia’ has to be calculated (by using the disk mass and the outer radius). The density of the flywheel material also has to be considered.
Rimmed Flywheels
The main parts of a rimmed flywheel are its inner hub, outer ring (also known as the ‘rim’), and arms. Generally, rimmed flywheels have 4-6 arms. A definite centrifugal force is exerted on the rims of the flywheel – and that generates tensile stress on it. The moment of inertia of the rim, along with the factor for the mass moment of inertia, are important parameters of rimmed flywheels.
The detonation of rimmed flywheels happens at a significantly lesser rotary speed than that of solid disk flywheels (other things remaining the same, like diameter, weight, etc.). The top flywheel manufacturers in India make sure that the rimmed flywheels they deliver are relatively lightweight, and have excellent energy-carrying capacities. The thickness at the center can be higher, to provide greater mechanical strength to the flywheel.
In terms of angular velocity (or, rakish velocity), flywheels can be classified as under:
High-Velocity Flywheels
The rakish speed of high-velocity flywheels generally varies in the 30K rpm and 60K rpm range. If required, this velocity can be increased to a certain extent. The user-friendly and lightweight nature of these flywheels is one of the biggest reasons behind their popularity. The cost of high-velocity flywheels is usually higher than that of low-velocity flywheels.
In order to bolster the user-convenience factor, the best flywheel manufacturers in India use powerful magnetic levitation bearings in their high-velocity flywheels. These tools have excellent durability and require minimal maintenance. The capacity, size, and other attributes of these flywheels can be customized by the manufacturers as per buyer needs.
Low-Velocity Flywheels
As their name suggests, the angular velocity of low-velocity flywheels is significantly lower than their high-velocity counterparts (generally, the maximum speed of these flywheels is 10K rpm). While they are relatively cheaper in terms of cost, the huge size of low-velocity flywheels can prove to be a challenge. The top suppliers help their clients set these up correctly, for optimal performance.
Unlike high-velocity flywheels, a low-velocity flywheel does not have handy levitation directional features. In addition, the latter also requires support on an intermittent basis. When installed correctly (generally, with additional construction support), low-velocity flywheels deliver efficient and economical performance. Buyers should get the different parts of these flywheels inspected from time to time.
The top flywheel manufacturers in India, like Crescent Foundry, have both single-mass and dual-mass flywheels in their portfolio. Let us take a look at the main points of difference between the two:
Single Mass Flywheels
Single mass flywheels are manufactured with a single piece of casting material, and they do not have any movable pieces. They facilitate fast-revving of engines and help to maintain a stable connection between the engine and the clutch assembly system. The enhanced warp resistance and thermal resistance of single mass flywheels are big advantages – and these flywheels can withstand sudden changes in gear and engine speed.
Durability is one of the most important features of any flywheel variety. Single mass flywheels are resurfaced as and when required, in order to boost their overall reliability and service life. Their cost is relatively lower as well. However, excessive vibration and noise can be a problem associated with using these flywheels.
Dual Mass Flywheels
There are two separate flywheels in a dual-mass flywheel – the first fitted to the clutch, and the other to the crankshaft. These flywheels have very good weight capacities (up to 50 kg) and monthly capacities. Diesel vehicles that are rather large in size and have manual transmissions generally use dual-mass flywheels (select petrol vehicles use them too). The strong springs in the flywheels minimize torsional spikes and keep the gearbox protected.
In order to keep noises and vibrations during operation low, dual mass flywheels come with powerful energy storage and transmission capabilities (to the crankshaft). As a result, the rotations between the piston pulses become a lot smoother. Since dual-mass flywheels optimally utilize engine power, fuel-efficiency levels are maximized. These flywheels cannot be resurfaced, however.
By the end of 2027, the value of the worldwide flywheel industry will zoom to just a shade under $242 million. Keeping pace with global trends, the Indian flywheel sector is growing fast as well – and the top flywheel manufacturers in India are regularly upgrading their portfolios and customizing their products, to ensure superior performance and longevity. The popularity of these revolving wheels as energy storage systems is growing exponentially – and buyers need to select the ‘correct’ type of flywheels, based on their precise requirements.